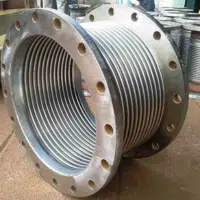
In the realm of industrial piping systems, expansion joints play a crucial role in accommodating thermal expansion, vibration, and misalignment. These components provide flexibility and reliability, ensuring the integrity and longevity of the system. Among the various types available, metal expansion joints stand out as versatile solutions, offering durability and resilience in demanding environments. In this comparative analysis, we delve into the characteristics and applications of metal expansion joints, particularly stainless steel bellows, and contrast them with other common expansion joint types.
Stainless steel bellows expansion joints, often referred to as high-temperature stainless steel bellows, are renowned for their exceptional performance in challenging conditions. These joints are constructed from multiple layers of stainless steel, meticulously welded to form a flexible and robust bellows structure. Their ability to withstand high temperatures, corrosive environments, and intense pressure fluctuations makes them a preferred choice across industries such as petrochemicals, power generation, and aerospace.
One of the key advantages of stainless steel bellows expansion joints is their unmatched durability. Unlike other materials that may degrade over time due to exposure to heat or chemicals, stainless steel maintains its structural integrity, ensuring long-term reliability. This durability translates to cost savings through reduced maintenance and replacement cycles, making stainless steel bellows expansion joints a cost-effective investment.
Pipe expansion joints, another common type of expansion joint, serve a similar purpose but are often constructed from materials such as rubber, fabric, or composite materials. While these joints may offer initial cost savings and flexibility, they lack the robustness and temperature resistance of stainless steel bellows. In high-temperature applications or environments with abrasive substances, pipe expansion joints may degrade rapidly, leading to leaks, downtime, and safety concerns.
Gimbal expansion joints, on the other hand, provide angular movement capability, making them suitable for applications where axial and lateral movement occur simultaneously. These joints consist of two sets of hinges that allow for controlled movement in multiple directions. While Gimbal expansion joints excel in certain scenarios, they may not offer the same level of flexibility or resistance to thermal cycling as stainless steel bellows expansion joints.
Exhaust bellows expansion joints and pump connectors expansion joints are specialized variants designed for specific applications. Exhaust bellows expansion joints are tailored for use in exhaust systems, where they absorb vibrations and compensate for thermal expansion in high-temperature environments. Pump connector expansion joints, meanwhile, are utilized to dampen vibrations and minimize noise transmission in pump installations. While these joints serve niche purposes effectively, they may not possess the versatility or resilience of stainless steel bellows expansion joints in diverse operating conditions.
In summary, while various expansion joint types exist to cater to different requirements, stainless steel bellows expansion joints emerge as the optimal choice for demanding applications. Their durability, temperature resistance, and versatility make them indispensable components in critical piping systems across industries. By investing in high-quality stainless steel bellows expansion joints, businesses can enhance system reliability, minimize downtime, and mitigate operational risks effectively.