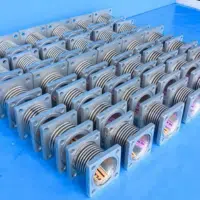
Are you looking to maximize performance and efficiency in your power generation equipment? Look no further than exhaust bellows. These often-overlooked components play a crucial role in maintaining and optimizing the performance of exhaust systems. By allowing for flexibility and absorption of vibrations, exhaust bellows help reduce stress on other components, improving longevity and reducing the risk of failures.
But the benefits of exhaust bellows don’t stop there. These specialized components also contribute to noise reduction, environmental compliance, and overall energy efficiency. By minimizing backpressure and optimizing the flow of exhaust gases, exhaust bellows ensure that your power generation operates at its peak performance while also reducing emissions and noise levels.
Whether you’re in the manufacturing, automotive, or marine industry, understanding the hidden benefits of exhaust bellows is essential for unlocking the full potential of your power generation equipment. In this article, we’ll delve deeper into the various advantages of using exhaust bellows, providing you with the knowledge you need to improve performance, enhance efficiency, and ensure the smooth operation of your industrial systems.
How exhaust bellows improve performance
Exhaust bellows play a vital role in improving the performance of your power generation equipment. One of the key ways they achieve this is by reducing backpressure in the exhaust system. Backpressure occurs when the exhaust gases encounter resistance as they try to exit the system. This resistance can lead to a decrease in engine power and efficiency. By incorporating exhaust bellows into your system, you can minimize backpressure and allow for a smoother flow of exhaust gases.
In addition to reducing backpressure, exhaust bellows also help optimize the flow of exhaust gases. Their flexible design allows for expansion and contraction, accommodating the natural movement of the engine and exhaust system. This flexibility ensures that the exhaust gases are efficiently expelled from the engine, helping to maintain optimal performance levels.
Furthermore, exhaust bellows play a crucial role in reducing the stress on other components within the exhaust system. The absorption of vibrations provided by the bellows helps to prevent damage and premature wear on components such as exhaust pipes and catalytic converters. By reducing stress and improving component longevity, exhaust bellows contribute to the overall performance and reliability of your power generation.
The role of exhaust bellows in reducing noise and vibration
Noise and vibration are common challenges in power generation equipment, and exhaust systems are no exception. The good news is that can help mitigate these issues. The flexible design of the bellows allows them to absorb and dampen vibrations caused by the engine’s operation, resulting in reduced overall noise levels.
Additionally, aid in reducing the transmission of vibration to other parts of the machinery. By absorbing and isolating vibrations, they prevent the transfer of these vibrations to surrounding components, minimizing the risk of damage and improving the overall smoothness of operation.
Furthermore, the reduction of noise and vibration provided by exhaust bellows has benefits beyond power generation performance. It contributes to a safer and more comfortable working environment for operators and nearby personnel. By reducing noise levels, exhaust bellows help prevent noise-induced hearing loss and promote overall workplace well-being.
Exhaust bellows and fuel efficiency
Fuel efficiency is a critical factor in any industrial application. The use of exhaust bellows can significantly contribute to improving fuel efficiency in your power generation. As mentioned earlier, exhaust bellows help reduce backpressure in the system. This reduction in backpressure allows the engine to expel exhaust gases more freely, resulting in improved engine efficiency.
By optimizing the flow of exhaust gases, exhaust bellows also aid in achieving a more complete combustion process. This means that fuel is burned more efficiently, extracting more energy from each unit of fuel consumed. The improved combustion efficiency directly translates to better fuel economy and reduced fuel consumption.
Furthermore, These can play a role in reducing the overall weight of the exhaust system. The lightweight and compact design of certain types of bellows minimize the system’s weight, reducing the load on the engine. A lighter exhaust system means less energy is required to move the machinery, leading to improved fuel efficiency.
Understanding the different types of exhaust bellows
Exhaust bellows come in various types, each designed to suit specific applications and requirements. It’s essential to understand the different types to choose the one that best matches your power generation needs.
- Single-ply bellows: These are the most common type of exhaust bellows, consisting of a single layer of metal that flexes to accommodate movement and absorb vibrations. They are suitable for most industrial applications and provide excellent performance and durability.
- Multi-ply bellows: Multi-ply bellows are constructed using multiple layers of metal, providing enhanced flexibility and durability compared to single-ply bellows. They are often used in applications where high levels of movement and vibration absorption are required.
- Reinforced bellows: Reinforced bellows incorporate additional reinforcement layers, such as wire mesh or external rings, to provide increased strength and resistance to pressure. These bellows are ideal for applications with high pressure or temperature requirements.
- Exhaust expansion joints: While not technically expansion joints serve a similar purpose. They are used in applications where significant movement and flexibility are required, such as in large power generation equipment or systems that experience thermal expansion.
When selecting an exhaust bellow, consider factors such as the operating conditions, temperature range, pressure requirements, and the specific needs of your power generation. Consulting with an expert or supplier can help you choose the most suitable type of bellows for your application.
Factors to consider when choosing exhaust bellows
Choosing the right exhaust bellows for your machinery involves considering several important factors. Here are some key considerations to keep in mind:
- Operating conditions: Assess the temperature range, pressure levels, and any corrosive or harsh environments the bellows will be exposed to. Ensure that the chosen bellows can withstand these conditions without compromising performance or durability.
- Flexibility requirements: Determine the level of movement and vibration absorption needed in your application. Choose a bellows type that provides the necessary flexibility to accommodate the anticipated movement and minimize stress on other components.
- Size and dimensions: Consider the space available for the bellows installation. Ensure that the chosen bellows can fit within the allocated space without obstructing other components or compromising functionality.
- Material selection: Select a bellows material that suits your specific requirements. Common materials include stainless steel, high-temperature alloys, and specialized coatings for corrosion resistance. The material should be compatible with the exhaust gases and the operating conditions of your power generation equipment.
- Supplier expertise: Partner with a reputable supplier or manufacturer with experience in exhaust bellows. They can provide guidance, technical expertise, and ensure that you receive a high-quality product that meets your needs.
By carefully considering these factors, you can choose the right exhaust bellows that will optimize performance, improve efficiency, and ensure the longevity of your machinery.